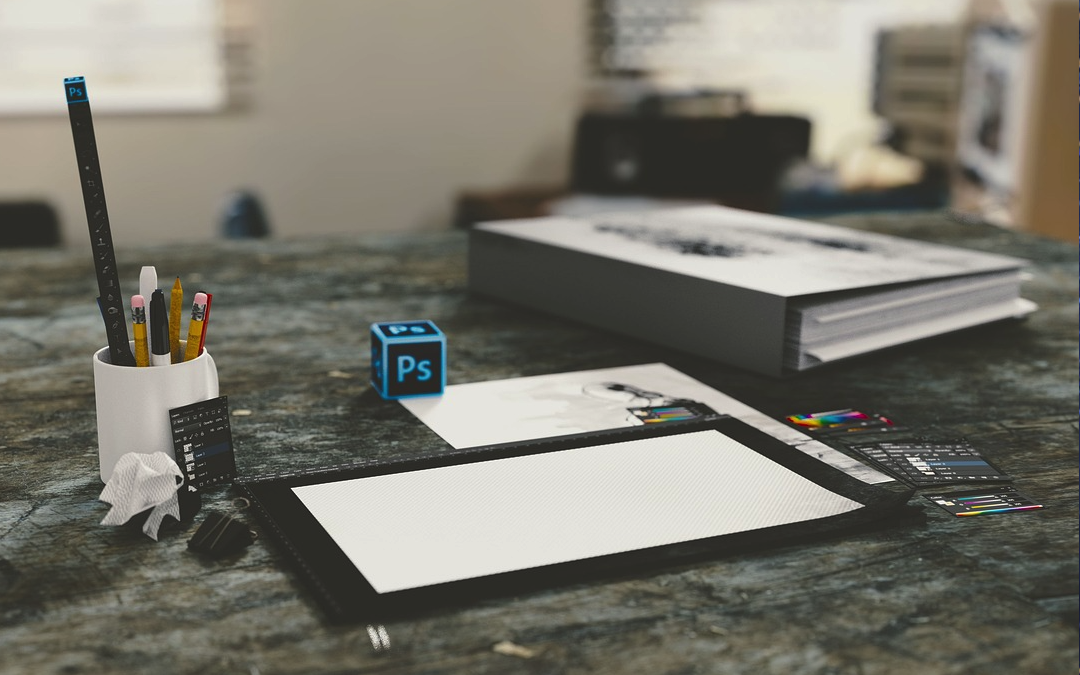
In today's hyper-competitive business environment, achieving peak operational efficiency is not just an advantage; it's a necessity. The lean philosophy, which focuses on maximizing value by minimizing waste, is pivotal for companies striving to enhance productivity and sustain profitability. Embracing this approach involves a comprehensive overhaul of processes and a dedicated commitment to continuous improvement.
This article outlines essential strategies and methods designed to guide businesses toward becoming as lean as possible. Whether you're running a startup or a multinational corporation, these tactics will help streamline your operations, reduce costs, and improve overall efficiency. By adopting these key strategies, businesses can better meet the demands of modern markets and ensure long-term success.
1. Embrace Lean Philosophy
Adopting a lean philosophy is the foundational step towards transforming your business into a lean operation. This approach focuses on value creation for the customer while minimizing waste. Waste can include anything that does not add value to the customer, such as unnecessary inventory, excess processing steps, or defects. By embedding this philosophy into your company culture, you ensure that every employee from top to bottom is focused on efficiency and value creation.
2. Implement Value Stream Mapping
Value Stream Mapping (VSM) is an indispensable strategy for businesses dedicated to maximizing efficiency and minimizing waste. This tool provides a visual representation of all steps in the process of delivering a product or service, from raw material to customer delivery.
By employing a value stream mapping template, organizations can standardize the process of mapping out their operations, ensuring consistency and clarity in identifying and understanding workflows. This visual approach helps pinpoint inefficiencies, such as unnecessary steps, delays, or redundancies that contribute to waste within the system.
Using a value stream mapping template enables teams to collaboratively and systematically analyze the current state of operations and envision a more streamlined future state. It facilitates deep insights into both material and information flows and highlights opportunities for improvement in areas such as cycle times, process bottlenecks, and service delivery. Ultimately, Value Stream Mapping is critical for any business aiming to implement lean practices effectively, as it directly contributes to enhancing productivity, reducing costs, and improving overall process efficiency. This method not only aids in decision-making but also fosters a culture of continuous improvement, driving businesses closer to becoming the leanest possible version of themselves.
3. Apply the 5S System
The 5S system, which stands for Sort, Set in order, Shine, Standardize, and Sustain, is a method used to organize and manage the workspace efficiently. Originally developed in Japan, the 5S system helps create a work environment that is clean, well-organized, and efficient. Implementing 5S helps reduce waste and optimize productivity by saving time and reducing errors. This system not only improves operational efficiency but also enhances safety and employee satisfaction.
4. Utilize Kanban
Kanban is a visual tool to manage work as it moves through a process. Kanban visualizes both the process (the workflow) and the actual work passing through that process. The goal of Kanban is to identify potential bottlenecks in your process and fix them so work can flow through it cost-effectively at an optimal speed or throughput. This method is very effective in promoting a smooth workflow and minimizing waste, especially in manufacturing and software development processes.
5. Focus on Continuous Improvement (Kaizen)
Kaizen, or continuous improvement, is a strategy where employees at all levels of a company work together proactively to achieve regular, incremental improvements to the manufacturing process.
This holistic approach involves finding inefficiencies, brainstorming solutions, and implementing simple fixes on a regular basis. Over time, these small adjustments lead to significant enhancements in productivity and quality. Kaizen encourages worker participation and fosters a culture of teamwork and ownership, which is essential for sustaining efficiency over time.
6. Optimize Inventory Management
Effective inventory management is crucial in a lean business. Overstocking leads to increased storage costs and risk of obsolescence, while understocking can result in missed opportunities and customer dissatisfaction. Techniques such as Just-in-Time (JIT) inventory can help by ensuring that inventory levels are kept as low as possible and goods are only received just in time to go into production or sales. This method reduces waste and frees up valuable resources for other uses.
7. Enhance Quality Control
To avoid the waste of redoing work, it’s crucial to get things right the first time. Enhanced quality control processes, such as Six Sigma or Total Quality Management (TQM), help identify and eliminate the causes of defects and quality issues in production. By improving quality control, businesses can reduce waste, lower costs, and improve customer satisfaction.
8. Streamline The Supply Chain
A lean supply chain is responsive, efficient, and customer-focused. Streamlining your supply chain involves coordinating all activities involved in sourcing, procurement, conversion, and logistics management. This can include renegotiating contracts to reduce costs, choosing suppliers closer to your business to reduce transportation costs, or integrating technology to improve procurement processes.
9. Adopt Technology and Automation
Technology and automation play crucial roles in modern lean strategies. Automation can take over repetitive, mundane tasks, allowing human workers to focus on areas that add more value. Meanwhile, technologies such as AI and data analytics can forecast trends and automate decision-making processes, which helps in optimizing operations.
10. Measure Performance and Set Benchmarks
Lastly, what gets measured gets managed. To truly lean your business, you need to measure performance across all processes. Use key performance indicators (KPIs) relevant to your lean objectives to track efficiency, quality, and customer satisfaction. Regularly compare these metrics against set benchmarks to identify areas for improvement.
Conclusion
Embracing lean principles is essential for any business aiming to streamline operations and increase efficiency in today's competitive landscape. By implementing the strategies outlined, such as Value Stream Mapping, the 5S System, Kanban, and continuous improvement through Kaizen, companies can significantly enhance their productivity and reduce waste.
These tools are not just methods but are transformative processes that integrate deeply within the fabric of your organization, fostering a culture of efficiency and quality. As businesses continue to navigate the complexities of modern markets, adopting these lean strategies ensures that they remain adaptable, responsive, and capable of delivering superior value to customers.
The journey to becoming the leanest possible business is ongoing—a commitment to continuous improvement and strategic adaptation that will pave the way for sustained success and operational excellence.
Share this post
Leave a comment
All comments are moderated. Spammy and bot submitted comments are deleted. Please submit the comments that are helpful to others, and we'll approve your comments. A comment that includes outbound link will only be approved if the content is relevant to the topic, and has some value to our readers.
Comments (0)
No comment